fonderie 1 PRÉSENTATION fonderie, technique et industrie de la fabrication d'objets métalliques obtenus par fusion puis moulage du métal.
Publié le 26/04/2013
Extrait du document
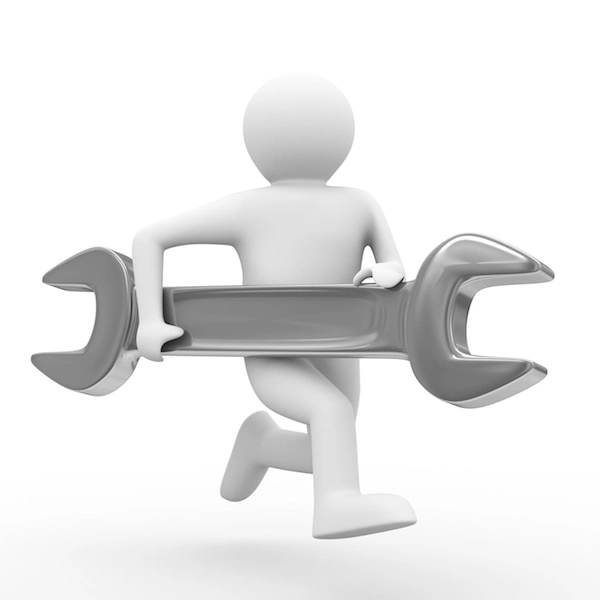
fonderie 1 PRÉSENTATION fonderie, technique et industrie de la fabrication d'objets métalliques obtenus par fusion puis moulage du métal. La fonderie est un art ancien dont on fait encore un usage considérable, même s'il a été dans une certaine mesure supplanté par d'autres méthodes, telles que la coulée sous pression, le forgeage, l'extrusion, l'usinage et le laminage. Voir Sidérurgie ; Métallurgie. La fonderie comporte trois opérations distinctes : la création d'un modèle en bois, plastique ou métal, réplique de l'objet fini ; la fabrication d'un moule creux ; la coulée du métal en fusion dans l'empreinte. Lorsque l'on produit un petit nombre d'objets, le modèle de fonderie est en général en bois verni, mais pour une production en grande série, il peut être en plastique, en fonte, en acier, en aluminium ou en un autre métal. Le modèle diffère de l'original sur deux points importants : les dimensions sont légèrement accrues afin de compenser le retrait du moulage lors du refroidissement et les modèles d'objets creux ont des saillies qui correspondent aux noyaux. Quoique les modèles puissent être monobloc, un moulage de forme complexe est plus facile à démouler si, lors de sa fabrication, on procède à sa fabrication par fonte de parties, assemblées ensuite. On attribue généralement une légère dépouille aux modèles des objets avec des côtés droits pour la même raison. Chaque partie est pourvue d'une cheville et d'un trou qui se correspondent pour assurer un alignement précis lors de l'assemblage. La description d'un moulage simple, un tuyau avec une extrémité à bride (figure 1), permet de comprendre la prise d'empreinte d'un modèle et la coulée d'un moulage. Le modèle pour ce moulage est représenté sur la figure 2. Les moules sont préparés dans des châssis (des boîtes en bois sans couvercle ni fond) équipés de chevilles et de dispositifs comme repères pour l'assemblage (figure 3). La boîte inférieure est appelée châssis du dessous et la boîte supérieure châssis du dessus. Afin de fabriquer le moule, on place la partie plate du demi-modèle sur une surface plane, on retourne le châssis du dessous et on le place autour de lui. Le sable de moulage est versé dans le châssis et foulé jusqu'à ce que le châssis en soit entièrement rempli. Le châssis est ensuite retourné et l'autre moitié du modèle mise en place, comme sur la figure 4. Une couche de sable étuvé spécial, appelé sable de séparation, est répandue sur la surface du châssis, puis le châssis du dessus est mis en place, rempli de sable et foulé. Les deux moitiés du moule sont ensuite séparées et le modèle est retiré. On perce alors une ou plusieurs vannes, ou trous de coulée à travers le sable du châssis du dessus, ainsi que des trous plus petits appelés évents, qui évacuent une partie de la vapeur qui se forme quand le métal chaud est versé dans le moule. Finalement, on prépare le noyau, la partie du moule qui donne sa forme à l'intérieur creux du moulage. Dans le cas du tuyau représenté sur la figure 1, ce noyau prend la forme d'un simple cylindre, mais un moulage complexe peut exiger un ou plusieurs noyaux. Les noyaux sont façonnés dans des boîtes à noyaux cloisonnées qui servent de modèles. Après façonnage, ils sont cuits dans un four jusqu'à ce qu'ils soient assez résistants pour être manipulés. Le noyau est placé à l'intérieur du moule (figure 5) et l'autre moitié du moule est remise en place. Dès lors, il est prêt pour la coulée. Après fusion dans un fourneau, le métal est versé à la main à partir d'un creuset pour les petits moulages ou, dans la plupart des cas, d'un grand seau basculant porté par une grue ou un chariot spécial, jusqu'à ce que le moule soit complètement rempli jusqu'en haut de la vanne. Après que le moulage a refroidi dans son moule, on secoue les châssis et on brise le moule. Les tiges de métal qui se sont formées dans les vannes et les évents sont ensuite enlevées, généralement sciées ou poncées. Le sable utilisé en fonderie contient suffisamment d'argile pour qu'une légère humidification avant usage lui donne de la cohésion. On utilise le sable de séparation pour que les châssis se détachent proprement quand on les sépare ; ce sable est sec et contient peu ou pas d'argile. On utilise le sable pour les moules, car il permet à une certaine quantité de vapeur et de gaz de s'échapper au moment de la coulée du moulage. Avec des métaux à point de fusion peu élevé, comme le laiton, il est possible d'utiliser des matériaux de moulage solides comme le plâtre de moulage. De tels moules -- ainsi que les moules métalliques -- présentent des surfaces plus lisses que les moules de sable et produisent ainsi des moulages plus détaillés et mieux finis. Ils ne peuvent cependant être utilisés pour mouler du fer ou de l'acier. La fonderie courante inclut de nombreuses variantes et techniques spéciales. Dans l'industrie, il n'est pas rare qu'on souhaite faire deux moulages ou plus dans un seul moule. Les modèles d'objets comportant des parties en surplomb peuvent être conçus avec des portions amovibles pour qu'on puisse retirer le modèle du moule sans remuer le sable. Lors du coulage de pièces mécaniques, telles que des engrenages, où la couronne doit être aussi dure que possible, des pièces de fonte ou d'acier appelées coquilles sont parfois placées dans le moule autour de la couronne. Bons conducteurs thermiques, les coquilles permettent à la portion du moulage à leur contact de durcir rapidement, ce qui rend le métal plus résistant. Les roues et les engrenages de grand diamètre sont parfois coulés sans châssis, dans des lits de sable directement sur le sol de la fonderie. Dans ce cas, la forme de la jante de la roue est taillée directement dans le sable et des noyaux sont placés dans le moule pour former le moyeu et les rayons. 2 MÉTHODES MODERNES DE FONDERIE Le moulage par centrifugation est une méthode adaptée pour couler des objets de forme circulaire, tels que des tuyaux métalliques. Pendant la coulée, on imprime une rotation rapide au moule circulaire ; il n'y a pas besoin de noyau car la rotation du moule plaque le métal par l'effet de la force centrifuge. Dans le moulage par enrobage -- une adaptation du procédé à la cire perdue de la fonderie de décoration --, le modèle est fabriqué en cire, souvent dans une installation de moulage en coquille, et revêtu d'une pâte aqueuse de matériau réfractaire qu'on laisse sécher. La coque réfractaire, avec le modèle en cire toujours à l'intérieur, est enfouie dans du sable et le moule passe au four. La cire fond et s'écoule, laissant le moule prêt à recevoir le métal. Les moulages obtenus par le procédé à la cire perdue donnent une bonne tolérance et reproduisent avec précision les petits détails. Dans le procédé de coulée continue, très répandu dans la production d'acier, de l'acier en fusion est versé à un débit constant au sommet d'un moule refroidi par eau de section uniforme, et de l'acier solide est retiré en continu de la base du moule. Microsoft ® Encarta ® 2009. © 1993-2008 Microsoft Corporation. Tous droits réservés.
Liens utiles
- automobile, industrie1PRÉSENTATIONautomobile, industrie, secteur de production industrielle englobant la conception, la fabrication et la commercialisation des véhicules automobiles.
- Mathématiques En plus / en moins Utilise la technique que tu veux pour dire combien il y a d'objets NOIRS en plus dans chaque ligne 25 18 45 36 60 53 100 76 100 48 Mathématiques COMBIEN?
- collage (art) 1 PRÉSENTATION collage (art), technique artistique consistant à agencer et coller sur un support donné (toile peinte ou non, papier, etc.
- all over 1 PRÉSENTATION all over, technique picturale de remplissage indifférencié de la surface du tableau, c'est-à-dire selon un mode de composition non hiérarchisé.
- aquatinte aquatinte, technique de gravure proche de l'eau-forte consistant à creuser à l'acide une planche de métal, afin de créer des tonalités plutôt que des lignes ; estampe imprimée par ce procédé.