sidérurgie - physique.
Publié le 24/04/2013
Extrait du document
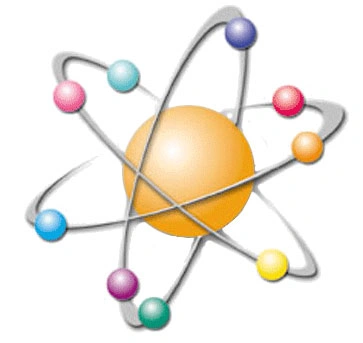
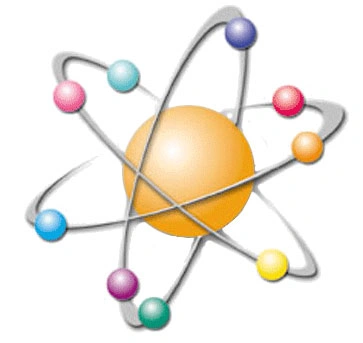
«
Lorsque, dans le minerai fondu, la teneur en carbone atteint le niveau désiré, le four est décrassé par un orifice situé à l’arrière.
L’acier fondu s’écoule alors dans un petittuyau de coulée en direction d’une grande poche placée sous le four au niveau du sol.
L’acier est versé de la poche dans des moules en fonte, qui forment des lingots.Récemment, des méthodes ont été mises en pratique pour fabriquer en continu de l’acier sans passer par le procédé de fonte des lingots.
4.2 Procédé à l’oxygène
Le procédé d’affinage du fer fondu par insufflation d’air fut mis au point par le Britannique Henry Bessemer, qui créa le four Bessemer, ou convertisseur Bessemer, en 1855. Ce procédé utilisait un four piriforme (cornue), qui pouvait être incliné sur le côté pour le chargement et l’évacuation.
De grandes quantités d’air étaient insufflées dans la masse de métal fondu.
L’oxygène se combinait alors avec les impuretés et les amenait à l’extérieur.
Aujourd’hui, on a amélioré ce procédé en remplaçant l’air par un courant d’oxygène haute pression pratiquement pur.
Des milliers de mètres cubes d’oxygène sontintroduits dans le four à l’aide d’une lance et se combinent avec le carbone et d’autres composés non désirés.
Il se produit alors une réaction à haute température, quiprovoque la calcination rapide des impuretés de la fonte et la transforme en acier.
Le procédé d’affinage dure au plus cinquante minutes, et environ 275 t d’acier peuventêtre produites en une heure.
4.3 Affinage au four électrique
Dans certains fours, la chaleur nécessaire à la fusion et à l’affinage de l’acier est fournie par l’électricité et non par le feu.
Les fours électriques sont particulièrementappréciables dans la production d’aciers inoxydables et d’aciers nécessitant des teneurs rigoureuses, le contrôle étant plus précis que dans un four Martin ou dans unconvertisseur à soufflage d’oxygène.
L’affinage est réalisé dans une chambre étanche fermée, où les conditions de température et de pression sont maintenues souscontrôle strict par des appareils automatiques.
Pendant les premières phases du procédé, on injecte de l’air enrichi en oxygène au moyen d’une lance, élevant ainsi latempérature du four et réduisant le temps nécessaire à la production de l’acier fini.
La quantité d’oxygène qui pénètre dans le four est rigoureusement contrôlée, dans le butde freiner les réactions d’oxydation non désirées.
Le plus souvent, la charge se compose presque entièrement de déchets.
Avant d’être utilisés, ils doivent être analysés et triés, car leur teneur en alliage affectera lacomposition du métal affiné.
D’autres matières, comme de petites quantités de minerai de fer et de chaux sèche, sont ajoutées afin de contribuer à l’élimination du carboneet autres impuretés.
Ils sont introduits dans la charge ou, plus tard, dans l’acier affiné lorsqu’il est versé dans la poche de coulée.
Lors de l’alimentation du four, on place des électrodes près de la surface du métal.
Le courant traverse l’une des électrodes, provoquant un arc électrique au niveau de lacharge métallique.
Cet arc traverse le métal et fait jaillir un autre arc sur l’électrode suivante.
La chaleur qu’il produit provoque la fusion rapide du métal.
4.4 Autres méthodes d’affinage du fer
La quasi-totalité de l’acier fabriquée dans le monde est issue de la fonte brute produite dans les hauts-fourneaux.
Il existe cependant d’autres méthodes d’affinage du fer.L’une d’elles consiste à fabriquer directement du fer et de l’acier à partir du minerai, sans passer par la fonte brute.
Dans ce procédé, le minerai de fer et le coke sontmélangés dans un four tournant et portés à environ 950 °C.
Le monoxyde de carbone présent dans le haut-fourneau est éliminé du coke chauffé avant qu’il ne réduise lesoxydes du minerai en fer métallique.
Le four produit alors un fer beaucoup plus pur que la fonte brute.
On peut également produire du fer pur par électrolyse ( voir Électrochimie), en faisant passer un courant électrique dans une solution de chlorure ferreux.
Voir aussi Acier ; Fer ; Métallurgie.
Microsoft ® Encarta ® 2009. © 1993-2008 Microsoft Corporation.
Tous droits réservés..
»
↓↓↓ APERÇU DU DOCUMENT ↓↓↓
Liens utiles
- Oral physique-chimie/maths: l'heure du crime !
- Niels Bohr: Physique atomique et Connaissance humaine
- devoir laboratoire physique chaleur massique
- TP n°11 Spécialité Physique-Chimie (Première) Mouvements et interactions Mouvements et forces
- Bac fiche révision physique